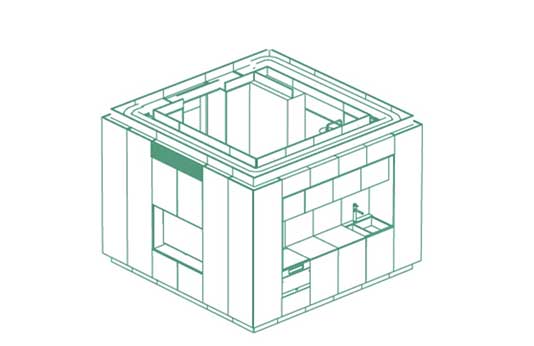
The Environmental Impact Clash: SAM vs Construction Tradition
In this article we want to discuss why we have to re-think the construction industry and how we intend to do it. We believe that SAM is just one of the many solutions needed to reduce the environmental impact of the built environment.
First, we will introduce you to SAM and explain the basic concepts it has been developed upon. Then, we will go through a very short analysis of the CO2 emissions of the built environment. Finally, we will breakdown the environmental impact of SAM and compare it to the traditional way of building homes. We’ll discuss how Bao Living, through its product, aims to innovate in the whole construction system and re-define the way we build living spaces.
Who is SAM?
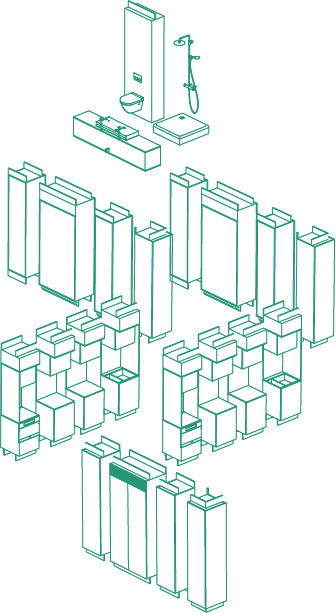
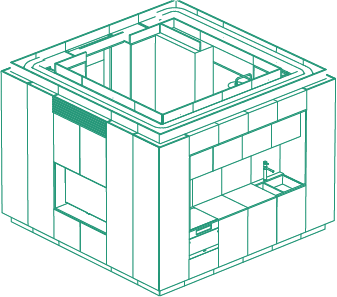
SAM is the Smart Adaptable Module developed and commercialized by Bao Living. It was born from the observation that the construction industry needs a paradigm shift if we are to survive the challenges of the 21st century, like climate change, rapid urbanization and digitization to name a few.
As its name suggests, SAM is a subtle mix of fixed building blocks and design freedom. It is made of prefabricated modules that can be combined in an infinite number of shapes and so adapted to any apartment geometry and size.
The other specificity of SAM is that it centralizes all the utilities you need in a home, this includes heating, ventilation, water supply and electricity. This enables a full de-coupling of the structure and the piping. I’ll tell you more about the advantages of this feature below.
The Impact of Construction Traditions
The built environment represents between a quarter and half of the CO2 emissions in the world [1][2] — the number depends on how the emissions are allocated to the various sectors. The CO2 emissions of a building can be separated into 2 main categories: embodied and operational. The embodied CO2 is emitted during the processing of materials and construction phase. It includes the excavation, processing and transport as well as the end-of-life of all the materials present in the building plus the waste produced on the way. The operational emissions happen during the use phase of a building. It depends on the type of energy source — renewables or fossil fuels — , the energy efficiency and finally the user’s behavior.
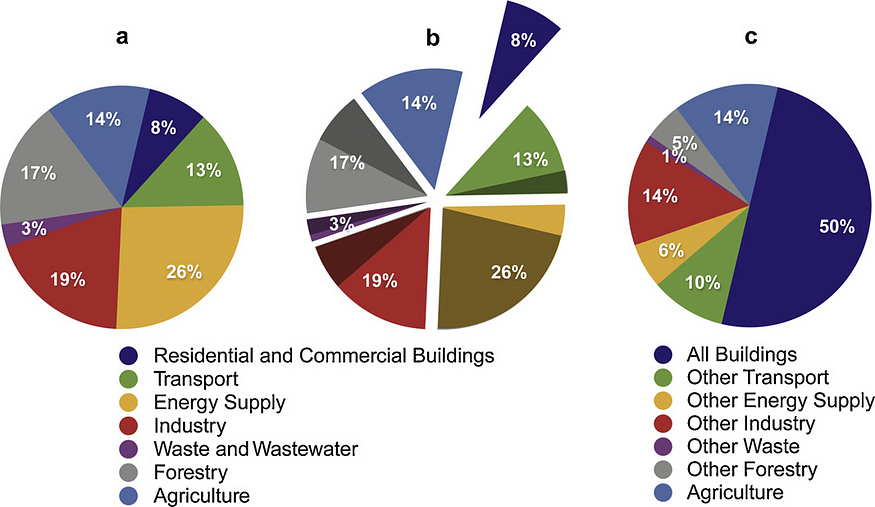
Traditionally, the operational emissions made up the biggest part of the CO2 cake. However, great progress has been made in thermal insulation and integration of renewable energies, making these technologies affordable. New regulations enforce their introduction, reducing the environmental impact of the use phase. Now, the research is looking into new materials and innovative construction methods to tackle the embodied CO2 of the built environment. There are different strategies to reach this goal: use less carbon intensive materials, use less material, produce less waste, expand life-time of object, re-use and re-cycle. Of course, the solution lies not in one way but in a tasty cocktail of all of them.
Materials & Circularity
Our modern buildings are mostly made of concrete and steel. Both these materials are very carbon intensive as they need very high temperatures during their production that only fossil fuels can provide. At Bao Living, we believe that wood is a great alternative. It has a very low environmental impact because, in contrary to concrete and steel, the tree it comes from has stored CO2 during its growth. Further, wood is especially easy to integrate in none-bearing structures like partition walls.
So yes, SAM’s structure is made of wood. By design, SAM replaces partition walls that would potentially be made of concrete or another more carbon intensive material and doing so saves embodied CO2. Thus, most of its positive impact comes actually from its intrinsic way to design homes combined to the choice of a renewable source of material.
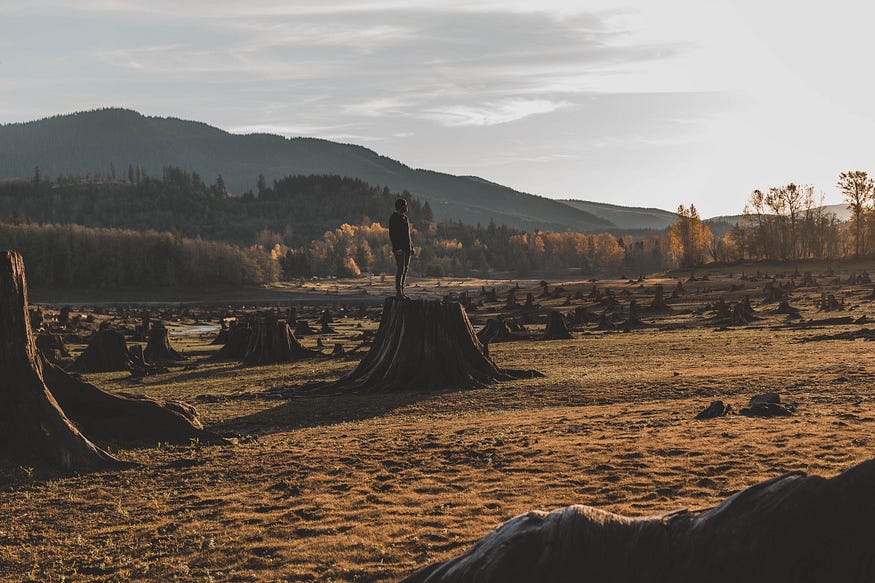
Even if wood is a renewable source of material, it is not safe from depletion. We have the duty to nurture our forests and to value the resources we gain from them. Thus, we should keep the wood that once made a SAM in the valuable material cycle as long as possible. That’s why we’re working on designing SAM for de-construction and circularity as much as possible. Our end-goal is to create a SAM that will be easily dismounted when its time comes, such that its parts will have the possibility to live on in new products or buildings. By taking the end-of-life phase of SAM into account in its design we want to avoid the depletion of raw materials and hence reduce our environmental bill a bit more.
Centralization & Decoupling
When presenting SAM I told you that it centralizes all the utilities you need in a home. This not only means that it provides heating, ventilation, water, electricity and automation, but that you won’t find any of those anywhere else in the apartment. By having them centralized we avoid the spreading out of pipes and wires and so save some more material and embodied CO2. We also have to note that in a traditional way of building, the (usually concrete) walls and floors have to be cut-out to install the wiring and piping. This traditional process produces waste material and makes recycling at the end-of-life of the building almost impossible. As SAM contains all the utilities in its own easy-to-dismount structure, we decouple them from the load-bearing building structure, thus avoiding more waste and enabling recycling.
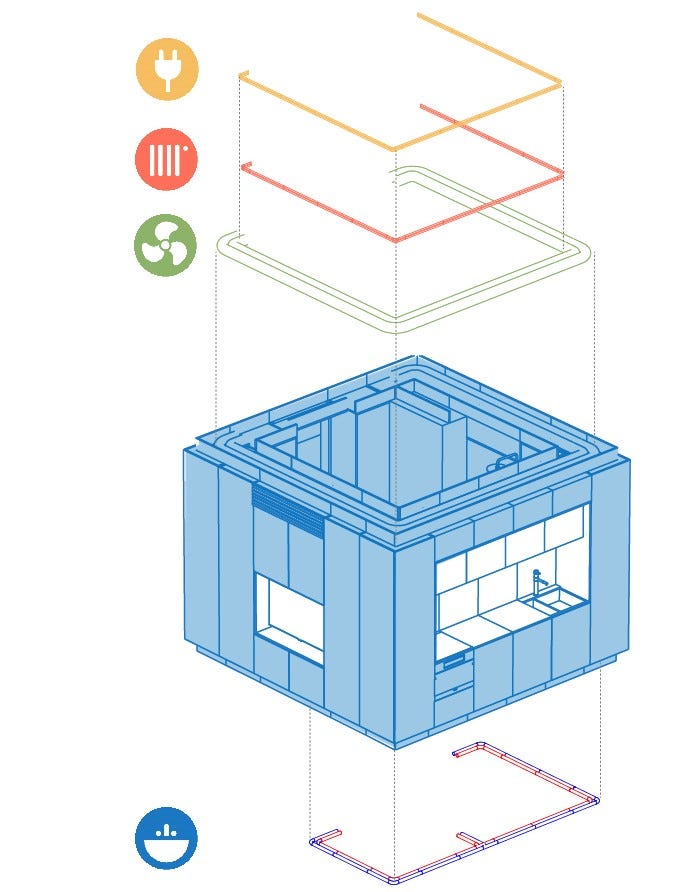
Decoupling the utilities from the building’s structure also means that their life-time are decoupled. With SAM, refurbishing a building becomes way easier. You can change the function of the interior without having to alter the structure. This new freedom in design prolongs a building’s life-time and so avoids waste from demolition and excavation of materials for a complete new building. If you want to know more about this topic, we invite you to read our previous article “Why simplifying a building’s structure is the surest way of lengthening it’s useful life”.
We talked about interior renovation and refurbishment, but SAM comes in very handy when you have to change your heating system as well. Indeed, it is equipped with convectors which are adaptable to both fossil fueled burners as well as renewable energies. In this way, you can wait for the “natural death” of your traditional system before transitioning to a heat pump, solar collectors or district heating.
Prefabrication & Modularity
At Bao Living, we believe that implementing a new design philosophy is not enough, we need to re-think the entire construction system. Nowadays, a tremendous amount of waste is produced on the construction site, mainly due to hand-made errors and miscommunication between parties. This is costly in term of material, time, and energy, but carries also a hidden cost for the environment since all three aspect are mostly based on fossil fuels.
To avoid errors on-site, we’re producing SAM in a controlled environment, it is pre-fabricated in an automated factory. This way of production enables us to reduce waste and increase the recycling rate. Further, it forces us to simplify our design, which not only makes cheap mass-production possible but also makes installation easier and faster. This means that we need less workers and less time than traditional construction methods, saving fossil fuel for transport of workers.
On the one hand, pre-fabrication is constraining our design freedom, since the size of our building blocks are fixed. But on the other hand, SAM has been designed with modularity in its core concept, which enables us to adapt it to any apartment morphology. Our building bricks may all be very similar to each other, but the number of combinations we can design with them is infinite. Hence, thanks to its design and mass-production, SAM can be integrated and adapted to a wide range of homes, making sustainable housing accessible and affordable for all.
Denser Living
When we broke down the CO2 emissions of the built environment, I mentioned that the operational part also depends on the user’s behavior. This is a very broad term that includes how we use our home, from heating to cooking, but also how much space per person we use. Indeed, the more space you occupy, the more heating power you need, hence the more CO2 you emit.
Combined to the rapid urbanization trend, this fact makes us believe that we need denser living solutions. To reduce the square meters per person, we must make use of every possible space. By replacing partition walls with SAM, we create storage amenities and free usable room for other functions, like a larger kitchen table to invite friends. In this way you use less gross floor for more usable space.
Closing word
Let’s recap the main points we discussed in this article. We first made the distinction between embodied and operational CO2 emissions of a building. We saw that SAM mostly tackles the embodied part by:
- using wood, a renewable source of material, as main building part instead of concrete or bricks
- aiming for circularity in its design (though we’re not quite there yet)
- enabling easier refurbishment by de-coupling the utilities from the load-bearing structure
- avoiding material and time waste through pre-fabrication
It also aims a reducing operational emissions by maximizing livable surface area in a small space through replacement of partition walls with storage room.
To conclude, SAM is not only an easy to plug-in solution, it is also an innovative way of re-defining the construction process as well as a modern urban housing philosophy. And through all these aspects we will do our part in creating a more sustainable built environment.
References
[1] International Energy Agency (IEA), “CO2 Emissions Statistics”, 2017. https://www.iea.org/statistics/co2emissions/
[2] F. Meggers, H. Leibundgut, S. Kennedy, M. Qin, M. Schlaich, W. Sobek, M. Shukuya, “Reduce CO2 from buildings with technology to zero emissions”, Sustainable Cities and Society, vol. 2, pp. 29–36, 2012. https://www.sciencedirect.com/science/article/abs/pii/S2210670711000618